Elevate Your Cosmetic Brand with ISO 22716 GMP Standards
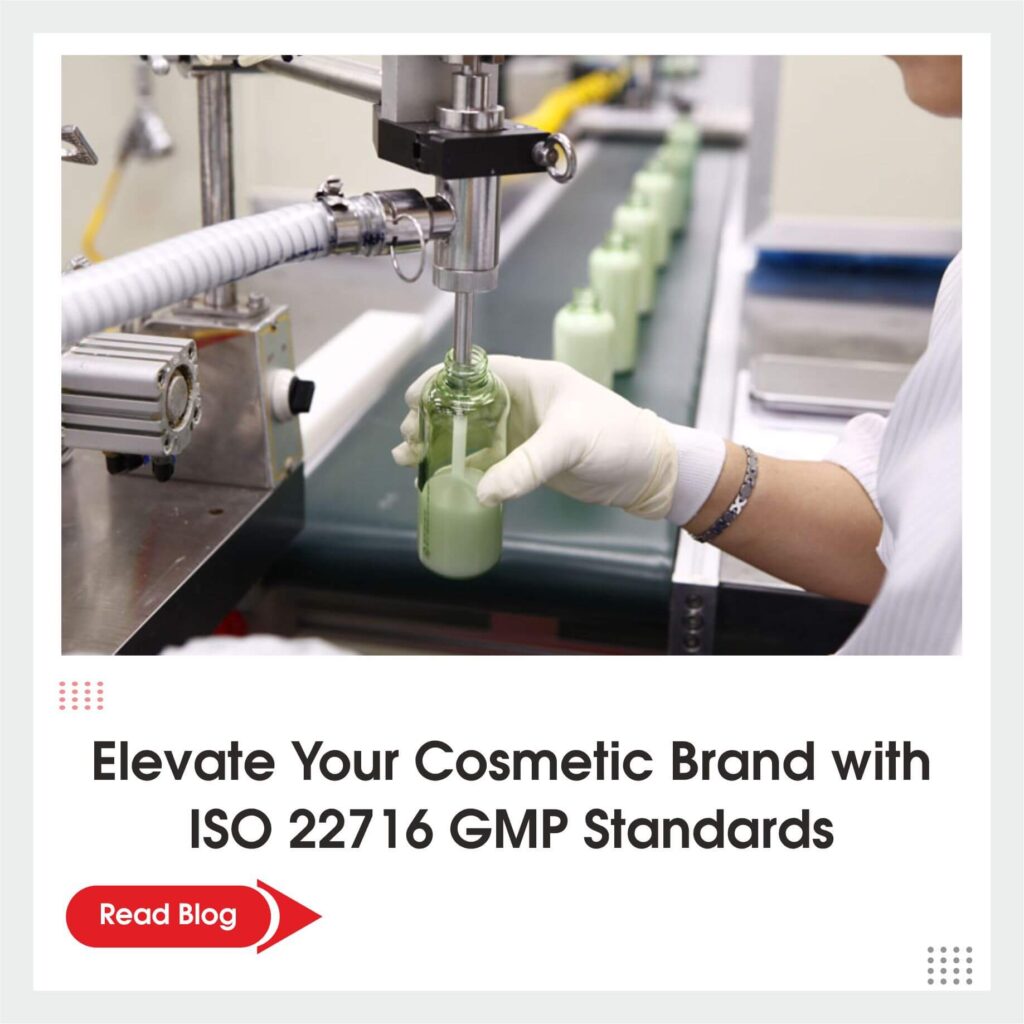
The ISO 22716:2007 standard considers the unique requirements of the cosmetic industry and has been designed for their consideration. The manufacturing, supervision, packaging, and distribution of cosmetics are the main topics of the standard. These recommendations include technical, administrative, and human resource management guidance that is both organized and useful in enhancing the quality of the final output. ISO 22716:2007 Good Manufacturing Practices in Cosmetics focuses on human, technological, and administrative elements that particularly impact product quality and contains a variety of applied consultation, working rules, and operational regulations. The goal of the ISO 22716:2007 standard is to identify actions that lead to an end product that fulfils the specified criteria, and hence product safety. Cosmetic producers can also be assured of satisfying international safety standards by adhering to ISO 22716. Demonstrating conformity with regulatory requirements across different markets, not only benefits the end-users but also promotes commerce. Importance OF ISO 22716:2007 Good Manufacturing Practice (GMP) ⮯ The International Organization for Standardization created Good Manufacturing Practices (GMP), which gives a comprehensive manual for the secure manufacture of cosmetics. ISO 22716:2007 standard was created and is being used by many countries. Under the headline, TS EN ISO 22716 Cosmetics – Good Manufacturing Practices (GMP) – Guidance on Good Manufacturing Practices, the Turkish Standards Institute (TSE) launched it in our nation. The ISO 22716:2007 standard describes a comprehensive quality management system strategy that covers the manufacturing, testing, packing, storing, and shipping of finished cosmetic goods. The ISO 9001 Quality Management System and the ISO 14001 Environmental Management System easily integrate with this standard. Advantages of Cosmetics Manufacturing Practices Under ISO 22716:2007 Good Manufacturing Practice (GMP)⮯ Ensure that the basic operational and environmental conditions needed to generate safe products are met by best industry practices. Make high-quality goods that are acknowledged and embraced globally. Obtain a competitive advantage over other market players. Make ensuring that products are safe for consumers to utilize. Naturally, businesses become more efficient in their operations as their expenses go down. EU COSMETICS GMP REQUIREMENTS ⮯ GMP, or good manufacturing practice, requirements for cosmetics form the core of the EU Regulation on Cosmetics. This law, which is intended to safeguard consumer safety, imposes stringent requirements on all European and non-European parties engaged in the supply chain of cosmetic products. Despite these legal requirements, all cosmetic products manufactured in the EU have to follow the ISO 22716:2007 standard’s Cosmetics Good Manufacturing Practices. Proof that the items are created by ISO 22716 can be provided by the ISO 22716 certificate or a declaration attesting to that fact. The following enumerates the domains for which ISO 22716:2007 stipulates certain requirements, together with their principal guidelines: Employees: employees should possess the necessary training to manufacture, oversee, and keep goods of a certain calibre. Premises: The location, layout, design, and use of the premises should guarantee product protection; allow for effective cleaning, sanitizing, and maintenance as needed; and reduce the possibility of product, raw material, and packaging unit mix-ups. Equipment: For equipment to be utilized for its original function, it must be able to be maintained, cleaned, and sanitized as needed. The equipment must be calibrated regularly in addition to being appropriately installed and cleaned. It should only be accessible and used by those who have been granted permission, and there should be enough backup procedures in place. Raw materials and packaging materials: raw materials and packaging materials that are purchased should meet defined acceptance criteria (physical, chemical, and microbiological) relevant to the quality of finished products. There should be proper measures and criteria in place for purchasing, receipt, identification and status, release, storage and re-evaluation of raw materials. The quality of water used in production should also be controlled. Production: steps should be performed at every level of the production and packaging processes to ensure that the final product has the specified qualities. Final products: The manufacturer must make sure that the products fulfill the specified acceptance criteria and are regulated using the approved test procedures before releasing them into the market. To preserve the quality of the final goods, care must be taken during storage, shipping, and return processes. Laboratory for quality control: The same guidelines that are outlined for staff, space, tools, subcontracting, and paperwork should also be applied to the lab. For materials to be released for use and products to be released for shipment, only when their quality meets the necessary acceptance criteria, the quality control laboratory must make sure that all relevant and necessary controls are carried out within its activity concerning sampling and testing. It is necessary to establish how a product that does not meet specifications is treated. Wastes: They need to be disposed of promptly and hygienically. Subcontracting: When it comes to subcontracting operations, a formal contract that is established, mutually confirmed, and controlled by both the contract giver and the contract acceptor is required. Deviations: Corrective action should be conducted after deviations have been found and enough data has been gathered about them. Recalls and complaints: The factory should evaluate, look into, and follow up on any concerns about the items that have been brought to their attention. Upon decision-making regarding a product recall, the necessary actions ought to be conducted to conclude the recall and execute the corrective measure. The procedure for handling complaints in contracted operations should be agreed upon by both parties. Change control: authorized staff must approve and carry out modifications that may have an impact on the product’s quality and do so only after gathering enough information. Internal audit: GMP implementation and status should be kept track of. Corrective measures should be suggested if needed. Documentation: An essential component of GMP is documentation. Depending on its organizational structure and product offerings, every business should have its document management system created, planned, implemented, and maintained. To avoid information loss, misunderstanding, etc., the documentation’s goal is to define the specified GMP activities.